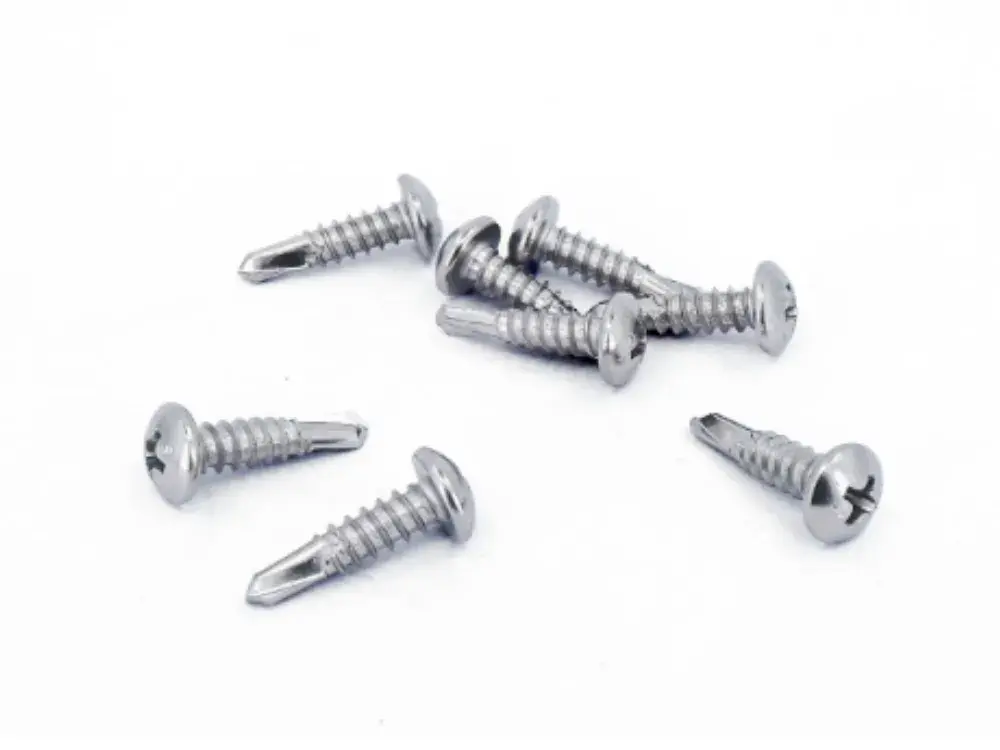
Pan head self tapping screws are built for reliable metal-to-metal connections. They come in a range of materials, drill point styles, and diameters to match specific fastening requirements. Used in sheet metal, enclosures, and HVAC assemblies, the pan head design distributes load evenly and enhances drive engagement.
How Self Tapping Pan Head Fasteners Work
Self tapping screws form their own threads during installation, removing the need for pre-drilled holes or tapped metal. Pan head versions are available in both thread-forming and thread-cutting designs. Thread-forming screws displace metal to create internal threads, while thread-cutting screws clear material using fluted or notched tips.
Installation success depends on choosing the right type for the job. Harder metals often call for cutting tips, while softer or thinner materials may benefit from thread-forming options. The broad pan head supports better bit alignment, helping reduce cam-out in fast-paced or automated settings.
Sizes, Diameters, and Dimensional Fit
Manufacturers produce pan head self tapping screws in multiple size families to support a wide range of application requirements. Standard diameters typically fall between #2 and #14, with metric equivalents such as M3 through M6 also available. These diameters are matched with corresponding thread pitches and lengths to ensure compatibility with metal gauges ranging from light-duty panels to structural enclosures.
The chart below outlines common diameters, drill point types, and application uses for selecting the right pan head self tapping screw.
*Head diameter and head height values are based on typical ANSI/ASME dimensional standards. Actual measurements may vary slightly by manufacturer or coating. Common thread pitches include 8–18 TPI for #8 fasteners and 10–16 TPI for #10, per standard pan-head size charts.
Proper length selection ensures sufficient thread engagement without excess protrusion. Head diameter and height must be carefully considered in applications where uniform panel seating and flush installation are important. Standard dimension charts for pan head self tapping screw sizes follow ASME or ISO tolerances, though specific manufacturers may offer slight variations.
Drill Points for Specific Metal Thicknesses
Drill point style plays a major role in fastener performance. Type A points are used with thin sheet metal and enable rapid engagement with minimal torque. Type AB provides hybrid performance suitable for general-purpose metal fastening. Self-drilling tips like #2 and #3 points can penetrate thicker metal substrates without a pilot hole, often up to 0.125 inches depending on material hardness.
Matching the drill point to the substrate thickness is essential to prevent stripping, misalignment, or sheared heads. In multi-layered assemblies or structural components, tip geometry must account for penetration depth and chip clearance.
Material Options for Strength and Corrosion Resistance
The chosen material affects how well the fastener resists corrosion and holds up in harsh conditions. Stainless steel self tapping screws pan head variants are frequently used in exterior or high-moisture environments where oxidation resistance is critical. 18-8 stainless is used for corrosion protection, while 410-grade alloys are selected when higher tensile strength is needed.
For indoor or low-exposure conditions, zinc-plated carbon steel provides reliable performance with moderate corrosion protection. Black pan head self tapping screws may feature oxide coatings or baked-on enamel finishes for visual discretion in electrical enclosures or assemblies with non-reflective requirements.
Application Areas for Pan Head Self Tapping Screws
Application areas for pan head self tapping screws include HVAC duct mounting, metal framing systems, steel enclosures, panel brackets, appliance housing, and signage installations. Each of these settings involves direct fastening to metal substrates where speed, precision, and surface retention are key.
In some retrofit applications, pan head fasteners are used to replace rivets or mechanical anchors, simplifying disassembly and ongoing maintenance. Their broad contact area reduces pull-through risk while enabling a uniform finish across mounting points.
Installation Considerations and Best Practices
Accurate torque control is necessary during installation, especially with thin metal substrates where material integrity can be affected. Overdriving the fastener can damage threads or deform the head. Use of torque-limited drivers helps maintain consistency and prevents failure. In automated setups, consistent head sizing and tip design help tools seat properly and ensure clean, reliable thread engagement.
Pre-drilling is not required when drill point and substrate thickness are properly matched. However, test fastenings are recommended for layered or unknown materials to verify performance before full installation.
Engineered for Precision in Every Application
Fastener Systems offers a range of pan head self tapping/piercing screws engineered for metal applications that require tight thread engagement and consistent drive control. Each fastener is manufactured to industry-tested tolerances for thread pitch, drive fit, and pullout resistance. Fastener Systems stocks both carbon steel and 410 stainless pan head self-drilling fasteners in Phillips drive configurations — supporting both indoor corrosion resistance and higher-hardness demands.
Get the Right Fit with Fastener Systems Pan Head Screws
Choose pan head screws designed for clean seating, reliable threading, and consistent performance in metal assemblies. We supply precision-built options that match real jobsite demands. Contact us today for more information.